案例研究
目前的批次方式在提高批量方面存在局限性。也考虑过切换到连续式,但没有相关的知识和经验…
行业:
可充电电池厂商 V公司
部门:
生产技术部
为了满足可充电电池大规模增产的需求,研究针对最重要工序的改进应开展哪些工作?
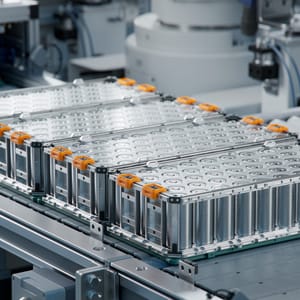
背景
由于电动汽车用可充电电池的需求不断增长,V公司已经连续几个月满负荷生产。为了满足进一步增长的需求,V公司正在研究大规模增产计划,但在这个过程中,一个课题显露了出来。
课题
想以最低的风险从批次方式切换到连续方式,但面临着很多的问题…
负责制定增产计划的生产技术部认为,在现有的电极生产线中,计量和混炼生产工序的创新是最为重要的。关于得出这一结论的理由,项目负责人R先生这样回顾。
“本公司在电极生产过程中,一直以来采用的都是将粉体材料按一定数量进行集中计量和混炼的批次方式。在采用批次方式的混炼工序中,随着批量的增加,混炼罐将会变得越来越大。但是,为了确保颗粒直径不同的多种材料能够均匀混炼,无法进一步加大混炼罐的容量。”
而且,采用批次方式时,更换品种和工序之间的搬运需要人工进行,很难实现生产效率的提升。
因此,R先生将目光转向了连续式电极生产方式。
“本行业的电极生产方式有从批次式切换为连续式的趋势。因为在采用连续式后,可以减少作业人员,大幅提高生产效率。因此,本公司也在考虑导入连续式电极生产工序。”(R先生)
但是,在收集信息的过程中发现,由于可充电电池行业大多采用保密性很高的技术,很难获取其他公司的生产技术的信息。另外,还存在如何确保可追溯性,以便在发生缺陷时排查影响范围的课题,而且,由于对改变生产方式的担忧,还有人提出了希望最大限度降低风险的意见。
鉴于这种情况,R先生所在的团队每天对需要采用哪种设备而烦恼不已。
课题的关键
采用批次方式的电极生产工序通过设备的大型化提高生产效率存在局限性
作为切换至连续方式、提高生产效率的决定性因素,难以获取所需设备等的信息
对连续方式存在担忧,例如发生缺陷时的可追溯性等